Component Repairs
TCT has in-house facilities to perform many Component Repair operations. Specifically for the Siemens Energy engine line, protective coatings are applied to both the internal and external components in order to minimize the detrimental effects of corrosion and erosion. The paints can be classified as a member of aluminium based corrosion resistant paints, stoving enamel grey, and dry film lubricants. A list of some of the paints that can be applied include PL101, PL163, PL165, PL205, PL237, PL239, Xylan 1010 (Teflon), Molykote D321R, Sermatel 570A, Sermatel 709, and Sermatel W. However, other coatings have been applied upon customer request. In addition to masking, painting and curing operations, other capabilities of the Component Repair department include blending and polishing, TIG welding and glass bead blasting.
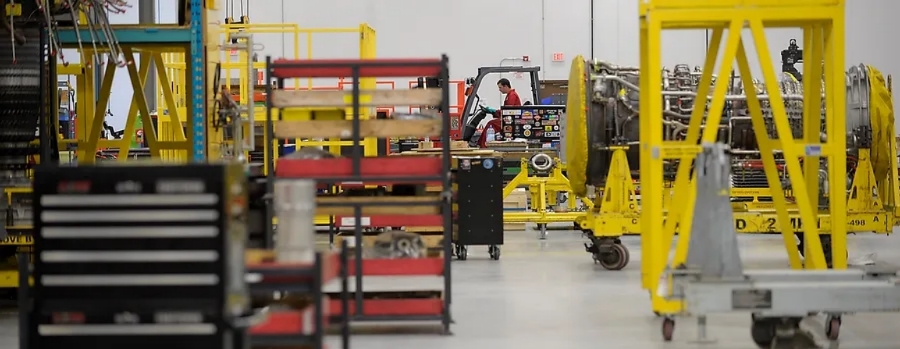
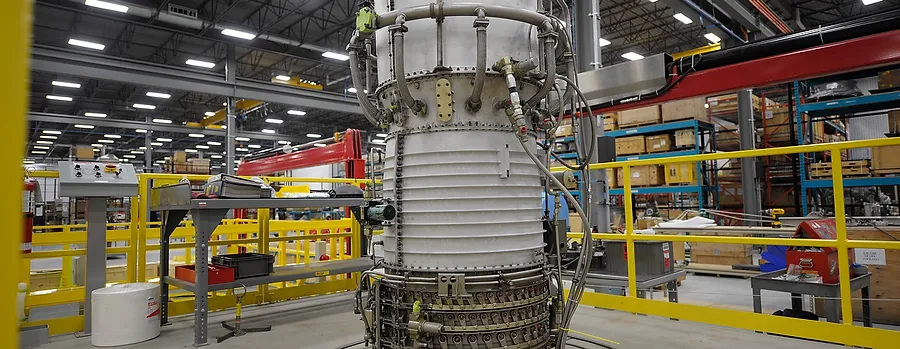
Service Agreements
TransCanada Turbines offers custom design support maintenance for each application of both General Electric & Siemens Energy engine lines. We will specifically support your needs, from a basic borescope to a complete overhaul and parts sale. Annual Routine Inspections (every 8,000 hours) consist of Borescope, visual inspection, and complete package & control calibration of components essential to reliable operation.
Scheduled Maintenance
TCT will manage, coordinate, and maintain the package on behalf of the Owner, in accordance with the established maintenance cycle of the equipment, policies, procedures, and laws.
These services include:
- Develop/implement routine, preventive and condition-based maintenance programs.
- Comprehensive reporting procedures are instituted to ensure close communications with the Owner.
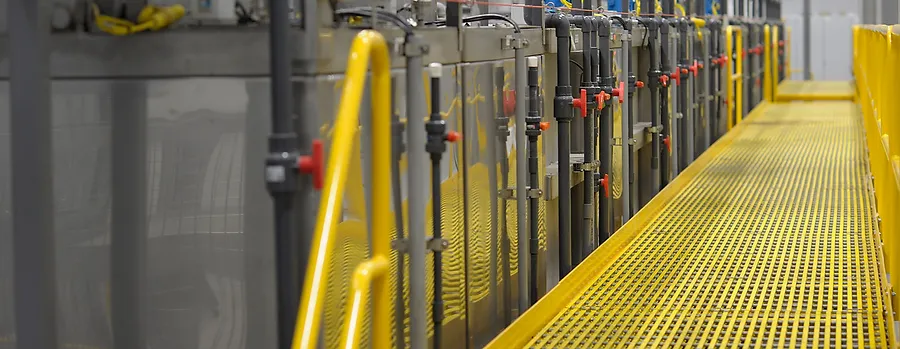
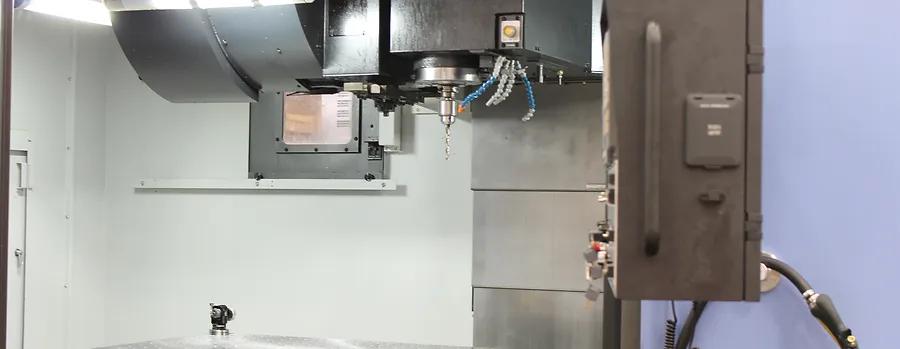
Major Maintenance
The various support services necessary during planned and unplanned maintenance outages of the covered gas generator will be delivered. The following paragraphs describe what these services are and how they are structured
Scheduled Maintenance activities include:
- Annual Routine Inspections (every ~8,000 hours) consist of Borescope, visual inspection, complete package and control calibrating of components essential to reliable operation.
- Hot Section Rotable Exchange - Performed at the site during a scheduled outage approximately every 25,000 hours of gas fuel operation.
-
Major Gas Turbine Overhaul - a complete overhaul of the gas turbine is performed at a Overhaul Depot approximately every 50,000 hours.
Key features of this overhaul are:- complete tear down and inspection of engine
- rebuild with new, refurbished and serviceable parts as required
- functionality and performance demonstration in the test cell.